Multi-Material Additive Manufacturing (MMAM) opens up a wide range of new applications. By having the freedom of choosing the material at a specific position, superior product properties can be achieved, designs can be more efficient and production lines can be shortened. Additionally, smart materials can be designed, which are actuated through differences in certain material properties, such as thermal expansion.
However, predicting the complex multi-physics (MM)AM processes remains problematic. The constantly changing domain, complex constitutive behaviour and wide range of time- and length scales make simulation of AM challenging. The Discrete Element Method (DEM) seems to be able to overcome these challenges. Since elements are free to be placed and moved, on element level interaction is relatively simple and DEM already requires small time steps. On top of that, DEM is suited well for simulating multi-material interaction and material interfaces naturally occur.
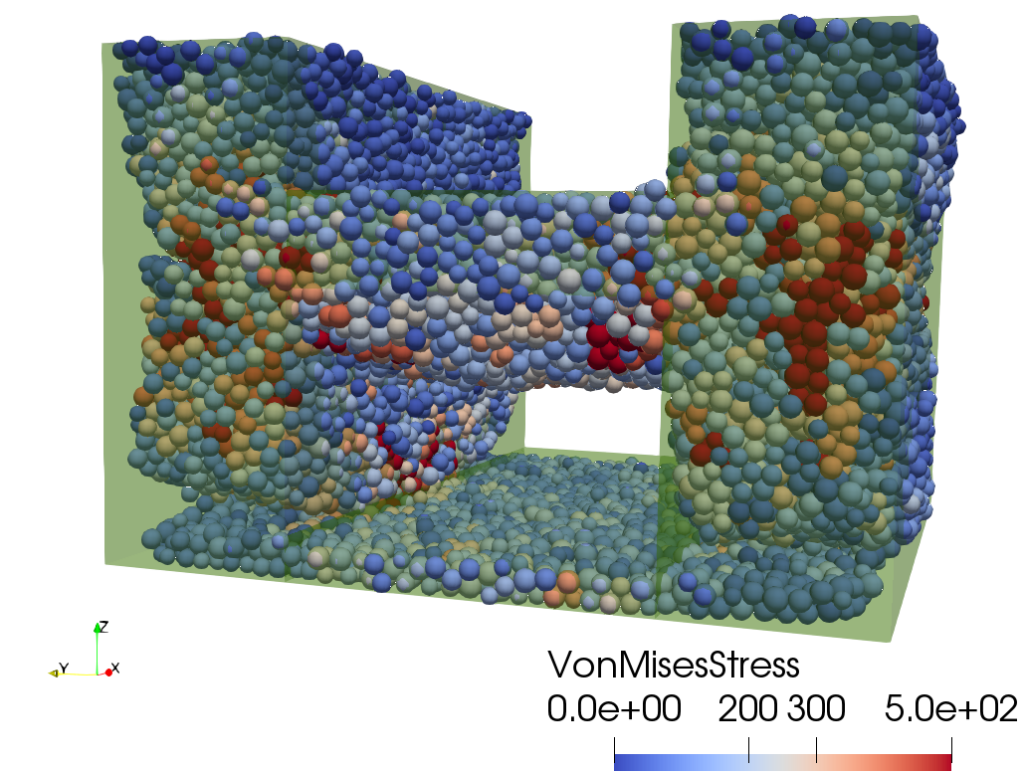
In this research a DEM framework is developed to gain more insight into the AM processes and predict product properties. The framework couples mechanical and thermodynamical analysis and is able to simulate the constitutive behaviour of powder as well as solid material. Various AM aspects are included, such as: heat source, deposition, G-code, residual stresses and deformations. The DEM framework fully simulates an AM printing process from start to finish using only the printer settings and material properties as input.
Personnel: | Bram Dorussen, Marc Geers, Joris Remmers |
Funding: | BOM (Brabants Ontwikkelings Maatschappij) |
Project Partners: | Industrio, AMPC Solutions |
Links: | Brainport Industries Fabriek van de toekomst (in Dutch) |